For several decades, mosaic concreteUsed for flooring. Thanks to the increased resistance to wear and the widest decorative possibilities, its popularity does not fall today.
Today, concrete-mosaic floors can be found inadministrative buildings, shopping centers, children's educational institutions and other public facilities. Moreover, when creating interior design of luxury apartments, designers are increasingly using this kind of decoration. What is so good mosaic floors, how they are made and whether it is possible to carry out their installation with their own hands, will be considered in this article.
Brief description of liquid marble floors
Concrete-mosaic floors can be safely calleduniversal coating, since they are suitable for use in absolutely all types of premises. With their help, you can realize bold design ideas and give the interior a touch of luxury and elegance.

The main component of the mixture for the production of this coating is concrete, in which marble, quartz or granite crumb is added.
It is derived from waste from the production of various products made of natural stone.
Granular material preserves allThe qualities that solid rocks originally possess. Due to the special properties of the raw material, the coating is very durable, which makes it possible to use it even in production facilities.
As a rule, concrete floors are monolithic (solid) or separated. Also, for the arrangement of the decorative coating, concrete-mosaic slabs can be used.
Structure of the mosaic floor
Marble mosaic floors consist of two mainlayers. The lower layer is presented in the form of a conventional concrete screed made of cement-sand mortar. It fits on any rough ground (carefully compacted soil, reinforced concrete surface or reinforced screed). Usually, the thickness of the lower layer of mosaic floors is 2-3 cm, but in some cases this figure can reach 4 cm. For example, when installing water heating systems.

Decorative coating is made of concretemixture with the addition of stone crumbs. Its thickness varies within 1.5-3 cm. This index can vary depending on the size of the fraction of natural filler. Thus, the total thickness of the mosaic concrete floor can be from 3.5 to 7 cm.
Main advantages of coating
As it became clear, mosaic floorscharacterized by a beautiful appearance and excellent strength. However, this is far from all the positive aspects that this type of finish has. Its incontestable advantages also include:
- Resistance to moisture. The concrete mix perfectly transfers contacts with water, it is not subject to settling by fungi and bacteria.
- Ecological and unpretentiousness in care. The floor surface is easily cleaned frompollution. If necessary, even disinfectant solutions can be used. The composition of the coating does not include harmful components, so this finish is considered absolutely safe and hypoallergenic.
- Extensive color gamut. Thanks to the abundance of natural shades of natural filler on the floor, you can create a variety of patterns of different colors. Some masters manage to turn the floor into a real masterpiece.
- Resistance to burning and abrasion. Concrete-mosaic floors are practically notwear out. They do not form cracks (as a result of blows), they do not inherent abrasion. It is for these reasons that such coverage can often be seen in crowded places.
- Fire safety. Marble and granite chips, which are part of the mosaic mixture, do not burn at all and do not form sparks during impacts and friction.
Negative sides of the coating
Unfortunately, today there are no perfect materials that are completely devoid of negative qualities. We will become acquainted with the shortcomings and features of the mosaic covering.

- Like any stone surface, the mosaic floors are quite cold. Therefore before their installation it is necessary to pay due attention to insulation.
- Because the life of this type of finishlong enough, you should carefully select its pattern. It is recommended to give preference to a neutral, classical ornament, which will not go out of fashion for a long time and will not get bored.
- In the process of using mosaic floors, red spots may appear on their surface.
- The cost of natural fillers included inthe composition of the mixture is high enough, so the installation of a concrete-mosaic floor is not cheap. Also, the final price is affected by the degree of complexity of the chosen pattern. The cost of such sex starts from 1200 rubles. per square meter.
It is possible to significantly reduce costs by only oneway - pour the mosaic floors. The price for similar services of masters is high enough, therefore this decision will allow you to save a decent amount.
Let's see how to do this work with your own hands.

Necessary tools and materials
Before proceeding with installation, make sure that you have all the necessary tools at hand. Namely:
- concrete mixer or drill with a special nozzle;
- a container for mixing the working solution;
- construction vacuum cleaner;
- wire brush;
- Sander;
- Bulgarian;
- grinding wheels (made of felt);
- building level;
- a long rule;
- powder for polishing the finished surface.
So, let's see how the mosaic concrete floor is made. The technology of its filling implies the execution of works in several stages:
- thorough preparation of the foundation;
- installation of dividing elements (to create a pattern);
- preparation of the working mixture;
- floor pouring;
- Finishing.
Let's consider each stage in more detail.

Preparation of the substrate and mixing of the working solution
The base for pouring the concrete floor should be as flat as possible. It is better if it is a monolithic basement or a cement-sand screed.
Work is carried out in the following order:
- The surface is cleaned of dirt, debris and dust.
- All existing cracks, depressions and cracks should be covered or poured with a small layer of the leveling mixture. Particular attention is paid to the areas near the heating pipes.
- Далее поверхности придается шероховатость.The work is carried out using a manual or electric wire brush. This action is designed to ensure the best adhesion of the substrate to the decorative coating.
- Clean surface is spilled with water or treated with a primer.
- Now you need to determine the thickness of the future mosaic floor and make appropriate marks on the walls.
Then you can start mixing the solution. To do this you will need:
- cement (1 part);
- stone flour (1 part);
- coloring pigments (from 0.1 to 1.3 parts);
- water (0, 5 parts);
- stone chips of different fractions (1 part).
All dry ingredients mix well and gradually add water. The resulting mixture should be hard and sedentary.
Layout pattern and styling the mixture
Now you need to properly mark the base,on which will be poured concrete mosaic floor. The device of the rails is carried out in full accordance with the selected ornament. They are located on the same level and are fixed on the cement mortar.

For these purposes, any suitable materials. You can use pipes, metal profiles, polymer products, glass, aluminum slats and brass products.
Filling the floor involves the following works:
- An ordinary cement-sand mortar is mixed, from which the substrate will be poured. It is filled with a small layer and leveled.
- After the base is slightly compacted, you can begin to fill the decorative mixture.
- The finished composition is distributed over the cells (up to the level of separation elements), according to the intended pattern and smoothed with a vibrating plate or trowels.
- When the entire surface is well compacted and smoothed, you can get the separating bars, and fill the voids with a solution.
- The final freezing surface comesa week later. Up to this point it is necessary to ensure that it remains slightly wet. For best results, sprinkle it with water (1 time per day) and cover with polyethylene.
Grinding
At the final stage, concrete mosaic floors are sanded. This is necessary in order for the coating to acquire a glossy effect. The work can be started in a week from the moment of pouring the solution.
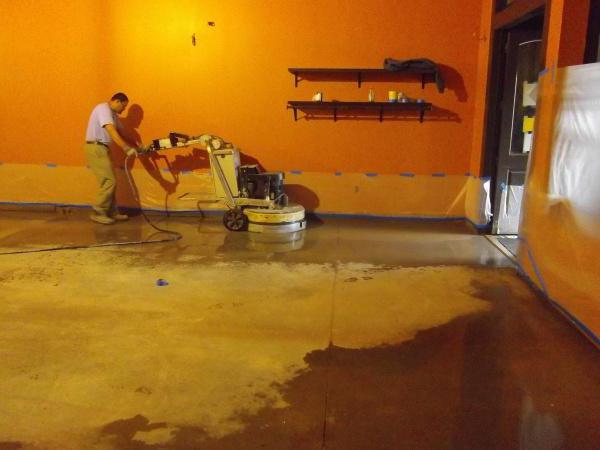
The surface is moistened with water and sprinkled with sand.In this way rough roughing of the upper layer is carried out. If in the process of work dents and voids are found, they are filled with cement mortar and rubbed with marble bars.
Final grinding is performed by specialmachine with felt nozzles and polishing powder. After the work has been done, the mosaic structure will become more visible, and the floor will look smooth and shiny.