To evaluate the performance properties of products andto determine the physical and mechanical characteristics of materials, various instructions, GOSTs and other regulatory and advisory documents are used. Recommended and test methods for the destruction of a series of products or similar samples of material. This is not a very economical method, but effective.

Characterization
The main characteristics of the mechanical properties of materials are as follows.
one.Temporary resistance or tensile strength - the force of the voltage, which is fixed at the highest load before the destruction of the sample. Mechanical characteristics of strength and plasticity of materials describe the properties of solids to resist irreversible changes in shape and destruction under the influence of external loads.
2The conditional yield strength is the stress when the residual strain reaches 0.2% of the sample length. This is the smallest voltage while the sample continues to deform without a noticeable increase in loads.
3The limit of long-term strength is the greatest stress, which at a given temperature causes the destruction of the specimen for a certain time. The determination of the mechanical characteristics of materials is guided by the limiting units of long-term strength — destruction occurs at 7,000 degrees Celsius per 100 hours.
four.The conditional creep limit is the stress that causes a given elongation at a given temperature for a certain time in the sample, as well as the creep rate. The limit is the deformation of the metal in 100 hours at 7,000 degrees Celsius by 0.2%. Creep is called a certain rate of deformation of metals with constant loading and high temperature for a long time. Heat resistance is the resistance of a material to destruction and creep.
five.The limit of endurance is called the greatest value of the stress cycle, when fatigue failure does not occur. The number of loading cycles can be specified or arbitrary, depending on how the mechanical testing of materials is planned. Mechanical characteristics include material fatigue and endurance. Under the action of loads in the cycle accumulate damage, cracks are formed, leading to destruction. This is fatigue. And the property of fatigue resistance is endurance.

Stretching and compression
Materials that are used in engineeringpractice, divided into two groups. The first is plastic, for the destruction of which significant residual deformations should appear, the second - brittle, collapsing with very small deformations. Naturally, such a division is very conditional, because each material, depending on the conditions created, can behave both as fragile and plastic. It depends on the nature of the state of stress, on temperature, on the rate of deformation and other factors.
Mechanical characteristics of materials atstretching and compression are eloquent in both plastic and brittle. For example, low-carbon steel is tested by stretching, and cast iron - by compression. Cast iron is brittle, steel is plastic. Fragile materials have greater resistance to compression, and tensile strain worse. Plastic materials have approximately the same mechanical properties of materials under compression and tension. However, their threshold is determined by stretching. It is with these methods that one can more accurately know the mechanical characteristics of materials. The diagram of stretching and compression is presented in the illustrations for this article.
Brittleness and ductility
What is plasticity and brittleness?The first is the ability to not collapse, receiving residual deformations in large quantities. This property is crucial for the most important technological operations. Bending, drawing, drawing, stamping and many other operations depend on the plasticity characteristics. Plastic materials include annealed copper, brass, aluminum, low carbon steel, gold, and the like. Bronze and duralumin are much less plastic. Almost all alloy steels are very slightly ductile.
Характеристики прочности пластичных материалов compare with the yield strength, which will be discussed below. The properties of brittleness and plasticity are greatly influenced by temperature and loading rate. Fast tension gives the material brittleness, and slow - plasticity. For example, glass is a fragile material, but it withstands a long-term effect of the load, if the temperature is normal, that is, it shows plastic properties. A low-carbon steel is plastic, however, with a shock impact load, it appears as a brittle material.

Oscillation method
Physico-mechanical characteristics of materialsare determined by the excitation of longitudinal, bending, torsional and other, even more complex types of oscillations and depending on sample sizes, shapes, types of receiver and pathogen, methods of attachment and schemes of application of dynamic loads. Large-sized products are also subject to testing using this method, if the method of application in the methods of applying the load, exciting the oscillations and registering them is substantially changed. The same method determines the mechanical characteristics of materials when it is necessary to evaluate the stiffness of large-sized structures. However, when locally determining the characteristics of the material in the product, this method is not used. Practical application of the technique is possible only when the geometrical dimensions and density are known, when it is possible to fix the product on supports, and on the product itself - converters, certain temperature conditions are needed, etc.
For example, when changing temperature conditionsthis or that change occurs, the mechanical characteristics of materials when heated become different. Virtually all bodies in these conditions expand, which affects their structure. Any body has certain mechanical characteristics of the materials of which it consists. If in all directions these characteristics do not change and remain the same, such a body is called isotropic. If the physico-mechanical characteristics of materials change - anisotropic. The latter is a characteristic feature of almost all materials, just to varying degrees. But there are, for example, steel, where the anisotropy is very small. It is most pronounced in such natural materials as wood. In a production environment, the mechanical characteristics of materials are determined by means of quality control, where different guests are used. Estimation of heterogeneity is obtained from statistical processing, when the test results are summarized. Samples should be numerous and cut from a specific design. This method of obtaining technological characteristics is considered quite time-consuming.
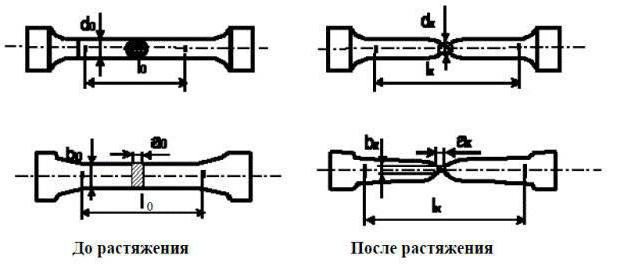
Acoustic method
Acoustic methods in order to determineThe mechanical properties of materials and their characteristics are quite numerous, and they all differ in the methods of input, reception and recording of oscillations in the sinusoidal and pulsed modes. Acoustic methods are used in the study, for example, of building materials, their thickness and state of tension, during defectoscopy. Mechanical characteristics of structural materials are also determined using acoustic methods. Numerous various electronic acoustic devices, which allow recording elastic waves and their propagation parameters both in sinusoidal and in pulsed mode, are already being developed and mass-produced. On their basis, the mechanical characteristics of the strength of materials are determined. If elastic oscillations of low intensity are used, this method becomes absolutely safe.
The disadvantage of the acoustic method isthe need for acoustic contact, which is not always possible. Therefore, these works are not too productive, if you need to urgently obtain the mechanical characteristics of the strength of materials. The state of the surface, the geometric shapes and dimensions of the product under investigation, as well as the environment where the tests are carried out, have a huge impact on the result. To overcome these difficulties, a specific task needs to be solved by a strictly defined acoustic method or, on the contrary, there are several to use them at once, it depends on the specific situation. For example, fiberglass is well suited to this study, because a good speed of propagation of elastic waves, and therefore is widely used through sounding, when the receiver and the emitter are located on opposite surfaces of the sample.
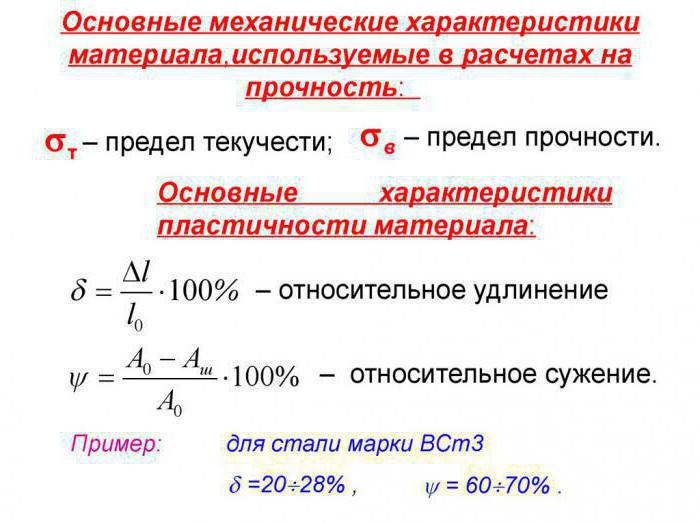
Flaw detection
Flaw detection methods are used to control the quality of materials in various industries. There are non-destructive and destructive methods. The following are non-destructive.
1. To identify cracks on surfaces and incomplete penetration magnetic flaw detection. Участки, которые имеют такие дефекты, characterized by dispersion fields. You can find them with special devices or simply put a layer of magnetic powder on the entire surface. On the ground of defects, the location of the powder will change as soon as it is applied.
2. Defectoscopy is performed using ultrasound. A directional beam will be reflected (scattered) differently if there are any discontinuities deep inside the sample.
3. Defects in the material shows well radiation research methodbased on the difference in absorption of radiation by a medium of different density. Used gamma flaw detection and X-rays.
4. Chemical flaw detection. Если поверхность протравить слабым раствором nitric, hydrochloric acid or a mixture of them (aqua regia), then in places where there are defects, the mesh appears in the form of black stripes. You can apply the method in which the sulfur prints are taken. In places where the material is not uniform, sulfur should change color.
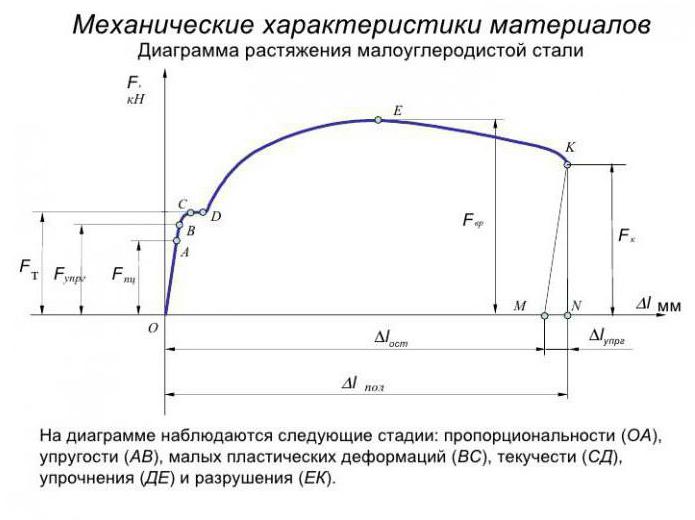
Destructive methods
Destructive methods here are already partially disassembled.Samples are tested for bending, compression, tension, that is, static destructive methods are used. If the product is subjected to variable cyclic loads on impact bending, dynamic properties are determined. Macroscopic methods paint a general picture of the structure of the material and in large volumes. For such research, specially polished samples are needed, which are etched. Thus, it is possible to identify the shape and location of the grains, for example, in steel, the presence of crystals with deformation, fiber, shell, bubbles, cracks and other alloying heterogeneities.
Microscopic methods are studiedmicrostructure and the smallest defects come to light. Samples in the same way pre-polished, polished and then subjected to etching. Further testing involves the use of electric and optical microscopes and X-ray diffraction analysis. The basis of this method is the interference of rays that are scattered by atoms of matter. The characteristic of the material is monitored using an x-ray analysis. The mechanical characteristics of materials determine their strength, which is essential for the construction of reliable and safe in operation structures. Therefore, the material is checked carefully and by different methods in all states that it is capable of accepting without losing a high level of mechanical characteristics.
Control methods
For non-destructive testingcharacteristics of materials is of great importance the correct choice of effective methods. The most accurate and interesting in this regard, the methods of inspection - defects control. Here it is necessary to know and understand the differences between the methods for implementing the flaw detection methods and the methods for determining the physicomechanical characteristics, since they are fundamentally different from each other. If the latter are based on the control of physical parameters and their subsequent correlation with the mechanical characteristics of the material, then flaw detection is based on the direct conversion of radiation that is reflected from a defect or passes through a controlled medium.
Best of all, of course, the control is complex.Complexity is to determine the optimal physical parameters by which you can identify the strength and other physical and mechanical characteristics of the sample. And at the same time, an optimal set of controls over structural defects is developed and then implemented. And finally, an integral assessment of this material appears: its performance is determined by a whole set of parameters that have helped to determine non-destructive methods.
Mechanical Testing
With the help of such tests are checked andevaluated the mechanical properties of materials. This type of control appeared a long time ago, but still has not lost its relevance. Even modern high-tech materials are often criticized by consumers. And this suggests that the examination should be carried out more carefully. As already mentioned, mechanical tests can be divided into two types: static and dynamic. The first ones check the product or the sample for torsion, tension, compression, bending, and the second - for hardness and impact strength. Modern equipment helps to carry out these not too simple procedures with high quality and to identify all operational properties of this material.
Испытанием на растяжение можно выявить material resistance to the effects of applied constant or increasing tensile stress. The method is old, tried and understood, used for a very long time and is still widely. The sample is stretched along the longitudinal axis by means of the device in the testing machine. The rate of stretching of the sample is constant, the load is measured by a special sensor. At the same time, the elongation is monitored, as well as its compliance with the applied load. The results of such tests are extremely useful if you need to create new designs, because so far no one knows how they will behave under load. Only the identification of all parameters of material elasticity can prompt. Maximum stress - the yield point is determined by determining the maximum load that a given material can withstand. This will help calculate the margin of safety.

Hardness test
Material stiffness is calculated in absolute value.elasticity. The combination of fluidity and hardness helps determine the elasticity of the material. If the technological process contains such operations as pulling, rolling, pressing, then it is simply necessary to know the amount of possible plastic deformation. With high ductility, the material will be able to take any shape with an appropriate load. A compression test can also serve as a method for identifying a safety margin. Especially if the material is fragile.
Hardness is tested with an indentor, whichmade of much harder material. Most often, this test is carried out according to the Brinell method (the ball is pressed), the Vickers (pyramid-shaped identifier) or Rockwell (a cone is used). The identifier is pressed into the surface of the material with a certain force in a certain period of time, and then the imprint remaining on the sample is studied. There are other fairly widely used tests: impact resistance, for example, when assessing the resistance of a material at the time of application of a load.