Good soldering is not as important as it is rightplacement of radioelements, but it also plays a significant role. Therefore, we will consider SMD installation - what is needed for it and how it should be carried out at home.
We stock up necessary and we prepare
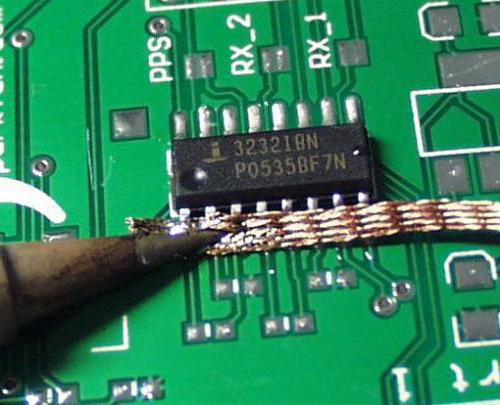
- Solder.
- Tweezers or pliers.
- Soldering iron.
- A small sponge.
- Side cutters.
First you need to plug the soldering iron into the socket.Then moisten the sponge with water. When the soldering iron heats up to such an extent that it can melt the solder, then it is necessary to cover it with (solder) sting. Then wipe it with a damp sponge. In this case, too long contact should be avoided, since it is fraught with hypothermia. To remove the remnants of the old solder, you can wipe the sponge stain (and also keep it clean). Preparation is also conducted in relation to the radio components. Everything is done with tweezers or pliers. For this, it is necessary to bend the terminals of the radio part so that they can enter the holes of the board without problems. Now let's talk about how to mount SMD components.
Getting started with details
Initially, you need to insert the components intoholes on the board that are intended for them. At the same time, make sure that the polarity is observed. This is especially important for elements such as electrolytic capacitors and diodes. Then you need to slightly dilute the terminals so that the part does not fall out of the set place (but do not overdo it). Just before starting the soldering, do not forget to wipe the sting with a sponge again. Now let's look at how SMD is installed in the home during the soldering phase.
Fixing parts

Checking the quality of work

- Ideally, the contact area and the output of the part must be connected. In this case, the solder itself should have a smooth and shiny surface.
- In the case of a spherical shape or presenceConnection with adjacent pads should heat up the solder and remove its excess. Consider that after working with it on the soldering iron tip there is always a certain amount of it.
- In the presence of a matte surface and scratches, melt the solder again and, without moving the parts, allow it to cool. If necessary, you can add it in a small amount.
To remove flux residues from the board, you canuse a suitable solvent. But this operation is not mandatory, because its presence does not interfere and does not affect the functioning of the scheme. Now let's pay attention to the theory of soldering. Then we will go through the peculiarities of each individual variant.
Theory

- It is necessary that the surfaces of the parts to be plastered are cleaned. To do this, it is important to remove all oxide films that form with time.
- The part must be heated in the place of soldering totemperature, which is enough to melt the solder. Certain difficulties arise when there is a large area with good thermal conductivity. After all, elementary may not have enough power soldering iron to heat the place.
- It is necessary to take care of the protection from the effects of oxygen. This task can be performed by colophony, which forms a protective film.
Most Common Errors

- The soldering points are touched by the tip of the soldering iron tip.At the same time, too little heat is supplied. It is necessary to apply the sting in such a way that the largest area of contact is created between the sting and the place of soldering. Then SMD montage will turn out qualitative.
- Used too little solder and agedsignificant time intervals. When the process starts, a part of the flux is already evaporating. The solder does not receive a protective layer, as a result - an oxide film. And how to properly mount SMD at home? To do this, professionals soldering seats are simultaneously pumped and soldering iron, and solder.
- Too early withdrawal of the sting from the place of soldering. It should be heated intensively and quickly.
You can take a capacitor for SMD mounting and fill it with a hand.
Soldering free wires
Now we will practice.Let's say we have an LED and a resistor. They need to solder the cable. In this case, no mounting plates, pins and other auxiliary elements are used. To accomplish this goal, you need to perform the following operations:
- Remove the insulation from the ends of the wire. They should be clean, because they were protected from humidity and oxygen.
- We twist the individual wires of the core. This prevents their subsequent shaking.
- Tin the ends of the wires. During this process, it is necessary to bring the heated up stinger to the wire together with the solder (which should evenly spread over the surface).
- We shorten the resistor and LED terminals. Then you need to zaludit (regardless of whether old or new parts are used).
- We hold the leads in parallel and apply a smallamount of solder. As soon as they are evenly filled with gaps, you must quickly remove the soldering iron. While the solder does not harden completely, you do not need to touch the part. If this still happened, then there are microcracks, which adversely affect the mechanical and electrical properties of the joint.
Soldering printed circuit boards

Now let's see how SMD happensinstallation in this case. Initially, the tip of the soldering iron and the solder are simultaneously led to the place of soldering. Moreover, the processed terminals and the board must be heated. It is necessary to hold the sting until the solder uniformly covers the entire contact area. Then it can be traced along a semicircle around the treated area. In this case, the solder must move in the opposite direction. We observe that it is evenly distributed throughout the contact area. After that, we remove the solder. And the last step is the rapid removal of the sting from the place of soldering. We wait until the solder gets its final shape and it stiffens. This is how SMD is installed in this case. The circuit board at the first attempts will not look so hot, but with time you can learn to do at a level that can not be distinguished from the factory option.