Construction of such design as a welding tabledo it yourself is the right decision. Thanks to this you get a place to work and practice. It should be noted that for the manufacture of devices better to take the metal. The tree will not work, as it is flammable.

Where to put the welding table with your own hands?In the garage it is put more often. Metal construction has many advantages. For example, it can be earthed, which ensures the safety of the master.

Functions of the welding table
Welding table with their own hands has a unified design. He is:
- a plane for work in which there are fixatives for workpieces;
- ground loop.
What tools and accessories will you need?
Many are interested in how to make a welding table with their own hands. This article will describe the process technology. An important point is the preparation of the necessary tools and accessories.
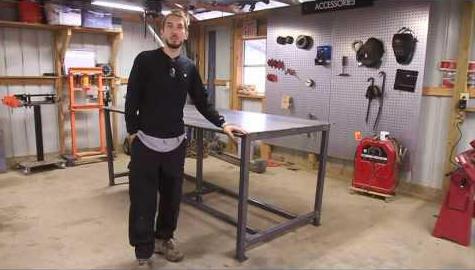
You will need:
- electric welding machine with all accessories (electrical cables, clips, electrodes, etc.);
- pliers;
- roulette;
- a piece of chalk;
- ruler;
- a hammer;
- three C-shaped clamps;
- a hacksaw for working with metal for cutting at the right angle (preferably using an electric grinder);
- the square is usual;
- square for carpentry work;
- nippers;
- tap to create thread M8;
- machine for milling or turning (it will be needed for chamfering parts).
Make a welding table with your own hands can be different. There are two models of the product.
First option
Self-made welding table, photo of whichpresented below, has a size of 1100x660x900 mm. So that the construction does not turn out to be too expensive and heavy, it is made of thick plywood sheet. In the future, it is covered with a plate of metal.

What materials will be required?

You will need:
- profile tube 40x20x2 mm - 9.9 m;
- steel strip size 40x4 mm - 2.0 m;
- four M8x40 bolts and four M8-6 nuts for fastening;
- one sheet of steel 1100x650x2 mm;
- one sheet of plywood 1220x1220x10 mm.
All materials must be free of corrosion. If there is rust, the surface should be skins. In order to make a welding table with your own hands, drawings are required.

Blanks
From the profile pipe size 40x20x2 mm are cut blanks:
- for the frame of legs and jumpers - two parts of 1.1 m each, two parts of 0.66 m each, four blanks of 0.9 m each, one part of 0.58 m;
- two blanks for foot jumpers of 0.58 m each;
- one part for a long foot jumper 1.02 m.
Chamfers are removed by milling or turning machine.
Welding frame for worktop
- Components of a profile pipe, necessary for welding the frame, are arranged and fixed by means of C-shaped clamps.
- The frame is a rectangle with a jumper. To check the correctness of the assembly, we recommend measuring two diagonal rectangles. The permissible error is no more than 1 mm.
- Billets under the frame are connected. First of all a rectangle is welded, and then - a jumper. First, a stitching seam is used, then a solid seam.
- Produced protective treatment grinder.
How to finish the countertop?
- The corners of the frame are enhanced by the overlays. For the purpose of fastening the legs and other mounted parts, a strip measuring 40x4 mm is used. Chamfers are removed. Finished parts are welded to the bottom corners.
- To fix the legs you need to weldlining of the strip. Drill the holes D <6 mm in the legs with a drill, then make similar holes D = 6.7 mm in the frame along them and cut the M8 thread. They should be attached, then weld the side rails.
- From plywood sheet must be cut out the tabletop. It is covered with a sheet of steel. If necessary, the layers are attached.
- We recommend treating all welds with anti-rust compound.
- Such designs as a homemade welding tablewith their own hands, can be given a modern look. This is achieved thanks to the attached wheels. So the fixture will be easier to move. The wheels need to be equipped with locking devices. On the table you need to install additional parts for fixing the workpiece. The holder for the welding torch can be welded to the upper corner. It can be made from a pipe of the desired diameter.
This design is quite large. It is suitable for welding large items.

The second option
The welding table with your own hands can be done differently. The second model has a size of 445x750x915 mm. This design is distinguished by compactness.
Required material
- Two plates of 445x750x3 mm.
- Four square 25x25x3 mm length 76 cm (their angle should be 45 degrees).
- Four corners of 32x32x3 mm, length 91.5 cm.
- One pipe D = 3 cm, the length of which is equal to 7.5 cm.
- Four support for wheels on the thread.
- Four nuts for the supports.
- Four nuts for connection.
- Four lock washers.
Stages of work
- Countertop frames and second shelves are welded. Two identical rectangles of 76 and 46 cm are prepared.
- Dimensions are checked. The tolerance is 1 mm.
- A sticking seam welds parts for the frame.
- Checks the correctness of the geometry.
- After that, all parts are welded main seam.
- The table top and the second shelf are welded. Initially, the connection is made with a stitching seam, and then solid.
- Legs are welded to the frame. They are fixed by means of clamps. They are attached at an angle of 90 degrees. Joints are welded with a point seam.
- In a similar way, legs are attached to the second shelf, located at a distance of 70 cm from the table top. After checking the geometric correctness, continuous seams are performed.
- Mounted wheel bearings.
- In the corner set the lock torch. A pipe D = 3 cm is used, the length of which is 7.5 cm.
What precautions exist?
Everyone knows that welding carries a certain amount of risk. To protect yourself from all troubles, you should follow a number of important recommendations:
- It is necessary to provide full ventilation of the work site. It is advised to install ventilation with an exhaust hood.
- Should be protected from electric shock. To this end, work should be carried out only in rubber gloves and ensure that they are not wet.
- Eyes should be protected from arc light. For this purpose, we recommend the use of helmets and goggles.
- Do not spray onto the desktop frommetal. Before welding, clean the place of work from debris. Particularly dangerous particles that are subject to easy ignition. If the work is carried out in the garage, then there should not be a container with paint, tanks with fuel nearby.
There are also special means for protection, without which the conduct of work is not recommended.