The word "encoder" is of English origin.It originated from the word encode, which means "transform." The most famous world manufacturers of these devices are such well-known brands as Siemens, SKB IC, HEIDENHAIN RLS, Baumer, SICK AG, Balluff, Schneider electric (Autonics Telemecanique), OMRON.

Scope and purpose of application
Encoder is a sensor used in industrialareas in order to convert the controlled quantity into an electrical signal. With it, it is determined, for example, the position of the shaft of an electric motor. Due to the fact that every device in which rotation is applied, must necessarily be equipped with a device that controls the accuracy of the torque, systems of exact displacement are popular areas of use of such transducers. The main purpose for which the encoder is used is to measure the angle of rotation of the object during rotation. Encoders are indispensable in the production process at machine-tool enterprises, in work-engineering complexes. They are also used in many modern measuring devices that need to register high-precision measurements of angles, rotation, turns and tilts.

Encoder Rankings
All currently known encoders are divided into absolute and incremental, resistor, magnetic and optical, working through industrial networks or bus interface.
Depending on the general principle of work, they distinguishabsolute encoders and incremental ones. The difference between these two types lies in the tasks they perform. The list of tasks for an absolute encoder is much wider than the list, which is covered by an incremental encoder.
Incremental Encoders
This is a pulse sensor.In the process of turning an object, pulses are fixed at its outputs, the number of which is directly proportional to the angle of rotation of the object. Usually, incremental transducers are used in the process of machine-tool construction in order to register the angular displacement of the shaft or in automated systems in the feedback circuit to measure and record the speed of rotation of the shaft.

Инкрементальный энкодер - это устройство, functioning on the basis of data pulses generated during rotation. The number of pulses per unit of turnover is the main operating parameter of this device. The current value is determined by the sensor according to the method of counting the number of pulses from the point of reference. In order to link the reference systems, reference tags are set on the pulse encoder, which are the starting marks after switching on the equipment. Data determination using an incremental transducer is only possible during rotation or rotation. When rotation is stopped, all encoder data is reset. As a result, when you next turn on the previous data counter will be unknown. For ease of use, the shaft should be reset. The incremental encoder perfectly copes with the task of measuring the speed of rotation. By counting the number of pulses from the reference mark, you can also accurately determine the current coordinate of the angle of rotation of the object.
Absolute Encoders
So called absolute position sensor.Usually in such encoders there are more complex processes of electronic signal processing and there is an optical scheme. But on the other hand, they give the details of the object immediately after switching on, which is often mandatory for the correct functioning of the system as a whole. Compared to incremental use of absolute encoders, it allows to solve a much wider range of tasks, since measurements are made not by fixing pulses, but by special digital codes. The unit of measure of such an apparatus is the number of unique digital codes per unit of rotation (1 revolution).

Absolute Encoder Types
Depending on the characteristics of the characteristicsThe absolute encoders can differ in the type of attachment, the presence of a blind or through, hollow or protruding shaft. The range of such devices is also very diverse in terms of external characteristics: length, case diameter, and so on. In addition, it is known that absolute sensors measuring position during rotation are multi-turn and single-turn. Single-turn produce the definition of the current coordinate within 1 revolution, and multi-turn capable of recognizing a few additional turns.
Optical encoder - what is it?
This converter is a hardmounted on the shaft disk made of glass. The optical encoder, in contrast to the sensors described above, is additionally equipped with an optical device, which in the process of rotating the shaft moves and converts the rotational moment into a stream of light, subsequently received by the photosensor.
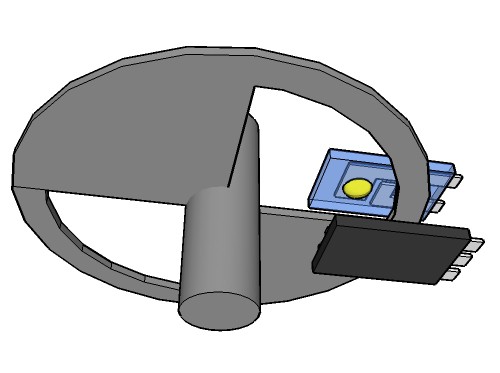
This type of transducer fixes the corners.rotation, where each unique position corresponds to a special unique code of numbers. He, along with the number of revolutions and is a unit of measurement of the sensor. The connection of the encoder and its principle of operation are identical to the operation of the incremental device described above.
Types of sensors depending on the principle of operation
According to the characteristics of the work encoders are divided into magnetic and photoelectric.
The physical principle of operation of the former is based onapplication of the Hall effect, opened in 1879 by E. Hall. In this case, the potential difference occurs only when the DC conductor is placed in the region of the magnetic field.
According to the characteristics of resolution and accuracy, the magnetic encoder is inferior to the photoelectric, but its implementation is simpler. It is much less demanding of the spaces and conditions of operation.
The representative of the magnetic encoder isis a device that fixes the cycle of passage of the magnetic pole of a rotating magnet located near the sensitive element. The data expression of the transmitter also has the form of a digital code.
A photoelectric encoder is a sensor,functioning on the basis of the photoelectric effect, which is observed as a result of the effect of light on a substance. This principle was discovered in 1887 by G. Hertz. In the process of the sensor of this type, there is a constant conversion of the light beam into an electrical signal.
