Aujourd'hui, il n'y a presque plus de domaines de la vie humaine,partout où la fonte est utilisée. Ce matériau est connu de l'humanité depuis longtemps et s'est révélé excellent d'un point de vue pratique. La fonte de fer est à la base d'une grande variété de pièces, d'assemblages et de mécanismes, et dans certains cas même d'un produit autosuffisant capable de remplir les fonctions qui lui sont assignées. Par conséquent, dans cet article, nous accorderons la plus grande attention à ce composé contenant du fer. Nous découvrirons également quels sont les types de fonte, leurs caractéristiques physiques et chimiques.
Définition
La fonte est un alliage vraiment unique de fer et de carbone, dans lequel Fe représente plus de 90% et C pas plus de 6,67%, mais pas moins de 2,14%. En outre, le carbone peut être en fonte sous forme de cémentite ou de graphite.
Le carbone confère à l'alliage une dureté suffisamment élevée,cependant, en même temps, il réduit la ductilité et la ductilité. Par conséquent, la fonte est un matériau fragile. En outre, des additifs spéciaux sont ajoutés à certaines qualités de fonte, qui sont capables de conférer certaines propriétés au composé. Les éléments d'alliage peuvent être du nickel, du chrome, du vanadium, de l'aluminium. L'indice de densité de la fonte est de 7200 kilogrammes par mètre cube. D'où nous pouvons conclure que le poids de la fonte est un indicateur qui ne peut pas être qualifié de petit.

Contexte historique
La fonte de la fonte est connue depuis longtemps par l'homme. La première mention de l'alliage remonte au VIe siècle avant JC.
En Chine, dans l'Antiquité, la fonte était obtenue à partir depoint de fusion assez bas. En Europe, la fonte a commencé à être produite vers le 14ème siècle, lorsque les hauts fourneaux ont été utilisés pour la première fois. À cette époque, cette fonte de fer était utilisée pour la production d'armes, d'obus et de pièces de construction.
La production de fonte brute est active en Russiea commencé au 16ème siècle et s'est ensuite développé rapidement. À l'époque de Pierre Ier, l'Empire russe a pu contourner tous les États du monde en termes de production de fonte, mais après cent ans, il a recommencé à perdre du terrain sur le marché de la métallurgie ferreuse.
La fonte de fer a été utilisée pour créerdiverses œuvres d'art même au Moyen Âge. En particulier, au 10ème siècle, les artisans chinois ont jeté une figure vraiment unique d'un lion, dont le poids dépassait 100 tonnes. Depuis le 15ème siècle en Allemagne, et par la suite dans d'autres pays, la fonte de fonte s'est généralisée. Des clôtures, des treillis, des sculptures de parc, des meubles de jardin, des pierres tombales en ont été fabriqués.
Dans les dernières années du 18ème siècle, la fonte de fer était la plus impliquée dans l'architecture de la Russie. Et le XIXe siècle était généralement appelé «l'âge de la fonte», car l'alliage était très activement utilisé en architecture.

Caractéristiques
Il existe différents types de fonte, mais la moyennele point de fusion de ce composé métallique est d'environ 1200 degrés Celsius. Ce chiffre est de 250 à 300 degrés inférieur à celui requis pour la fusion de l'acier. Cette différence est due à la teneur en carbone assez élevée, ce qui conduit à ses liaisons moins étroites avec les atomes de fer au niveau moléculaire.
Au moment de la fusion et de la cristallisation ultérieurele carbone contenu dans la fonte n'a pas le temps de pénétrer complètement dans le réseau moléculaire du fer, et par conséquent la fonte s'avère de ce fait plutôt fragile. Par conséquent, il n'est pas utilisé en présence de charges dynamiques permanentes. Mais en même temps, il est excellent pour les pièces qui ont des exigences de résistance accrues.
Technologie de production
Tous les types de fonte sont produits dans un haut fourneaufours. En fait, le processus de fusion lui-même est une activité plutôt laborieuse qui nécessite de sérieux investissements matériels. Une tonne de fonte nécessite environ 550 kilogrammes de coke et près d'une tonne d'eau. La quantité de minerai introduite dans le four dépendra de la teneur en fer. Le plus souvent, le minerai est utilisé, dans lequel le fer n'est pas inférieur à 70%. Une concentration inférieure d'un élément n'est pas souhaitable car son utilisation ne sera pas économiquement rentable.
Première étape de production
La fusion de la fonte brute est la suivante. Tout d'abord, du minerai est versé dans le four, ainsi que des grades de charbon à coke, qui servent à pomper et à maintenir la température requise à l'intérieur de la cuve du four. De plus, ces produits du processus de combustion participent activement aux réactions chimiques en cours en tant qu'agents réducteurs de fer.
En parallèle, le flux est évacué dans le four, servant de catalyseur. Il aide les roches à fondre plus rapidement, ce qui favorise la libération précoce du fer.
Il est important de noter que le minerai avant le chargement dans le foursubit un traitement préalable spécial. Il est broyé dans une usine de concassage (les petites particules fondent plus rapidement). Il est ensuite lavé pour éliminer les particules sans métal. Après cela, les matières premières sont cuites, de sorte que le soufre et d'autres éléments étrangers en sont retirés.

Deuxième étape de production
Dans un four chargé et prêt à l'emploile gaz naturel est fourni par des brûleurs spéciaux. Le coke réchauffe la matière première. Cela libère du carbone, qui se combine avec l'oxygène pour former un oxyde. Cet oxyde participe ensuite à la réduction du fer du minerai. Notez qu'avec une augmentation de la quantité de gaz dans le four, la vitesse de la réaction chimique diminue et lorsqu'un certain rapport est atteint, elle s'arrête complètement.
L'excès de carbone entre dans la fonte et entrecollage avec du fer, formant éventuellement de la fonte. Tous ces éléments qui n'ont pas fondu se retrouvent à la surface et sont finalement éliminés. Ces déchets sont appelés scories. Il peut également être utilisé pour fabriquer d'autres matériaux. Les types de fonte ainsi obtenus sont appelés fonte et fonte.
Différenciation
La classification moderne des fontes prévoit la division de ces alliages dans les types suivants:
- Blanc.
- Moitié.
- Gris avec graphite lamellaire.
- Graphite sphéroïdal haute résistance.
- Malléable.
Jetons un coup d'œil à chaque espèce séparément.

Fonte blanche
Une telle fonte est celle qui apratiquement tout le carbone est lié chimiquement. En génie mécanique, cet alliage n'est pas utilisé très souvent, car il est dur, mais très cassant. Il ne se prête pas non plus à l'usinage avec divers outils de coupe, et est donc utilisé pour la coulée de pièces ne nécessitant aucun traitement. Bien que ce type de fonte permette le meulage avec des meules abrasives. La fonte blanche peut être ordinaire ou alliée. Dans ce cas, le soudage lui pose des difficultés, car il s'accompagne de la formation de diverses fissures lors du refroidissement ou du chauffage, ainsi que du fait de l'hétérogénéité de la structure formée au point de soudage.
Les fontes blanches résistantes à l'usure sont obtenues parcristallisation primaire d'un alliage liquide lors d'un refroidissement rapide. Ils sont le plus souvent utilisés pour les applications de friction sèche (par exemple les plaquettes de frein) ou pour la production de pièces à résistance accrue à l'usure et à la chaleur (rouleaux de laminoir).
Au fait, la fonte blanche tire son nomen raison du fait que l'apparence de sa rupture est une surface lumineuse cristalline et rayonnante. La structure de cette fonte est une combinaison de ledéburite, de perlite et de cémentite secondaire. Si cette fonte est soumise à un alliage, la perlite se transforme en troostite, austénite ou martensite.

Demi fonte
La classification des fontes sera incomplète sans évoquer ce type d'alliage métallique.
La fonte spécifiée se caractérise par une combinaisoncarbure eutectique et graphite dans sa structure. En général, la structure à part entière est la suivante: graphite, perlite, ledéburite. Si la fonte est soumise à un traitement thermique ou à un alliage, cela conduira à la formation d'austénite, de martensite ou de troostite aciculaire.
Ce type de fonte est assez fragile, son utilisation est donc très limitée. L'alliage lui-même tire son nom du fait que sa rupture est une combinaison de zones sombres et claires de la structure cristalline.
Le matériau d'ingénierie le plus courant
La fonte grise GOST 1412-85 contient environ 3,5% de carbone, 1,9 à 2,5% de silicium, jusqu'à 0,8% de manganèse, jusqu'à 0,3% de phosphore et moins de 0,12% de soufre.
Le graphite dans une telle fonte a une forme lamellaire. Cela ne nécessite aucune modification particulière.
Les plaques de graphite ont un fort affaiblissementl'action et donc la fonte grise se caractérise par une très faible résistance aux chocs et une absence quasi totale d'allongement relatif (l'indicateur est inférieur à 0,5%).
La fonte grise fonctionne bien. La structure de l'alliage peut être la suivante:
- Ferrite-graphite.
- Ferrite-perlite-graphite.
- Perlite-graphite.
La fonte grise fonctionne beaucoup mieux pour la compression,plutôt que de la tension. Il se soude également assez bien, mais cela nécessite un préchauffage, et des tiges en fonte spéciales à haute teneur en silicium et en carbone doivent être utilisées comme matériau de remplissage. Sans préchauffage, le soudage sera difficile, car la fonte blanchira dans la zone de couture.
A partir de la fonte grise, sont produites des pièces qui fonctionnent en l'absence de chocs (poulies, couvercles, lits).
La désignation de cette fonte s'effectue selon le principe suivant: SCh 25-52. Deux lettres signalent qu'il s'agit de fonte grise, le nombre 25 est un indicateur de la résistance à la traction (en MPa ou kgf / mm2), le numéro 52 est la résistance ultime au moment de la flexion.
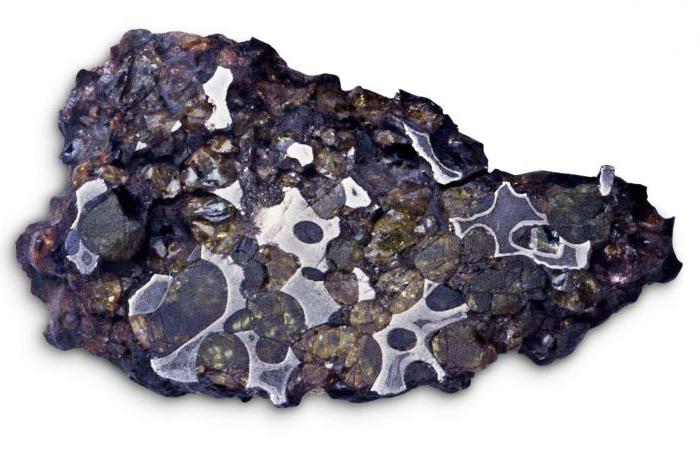
Fonte ductile
Fonte nodulaire en principediffère de ses autres "frères" en ce qu'il contient du graphite sphérique. Il est obtenu en introduisant des modificateurs spéciaux (Mg, Ce) dans l'alliage liquide. Le nombre d'inclusions de graphite et leurs dimensions linéaires peuvent être différents.
Pourquoi le graphite nodulaire est-il bon? Le fait que cette forme affaiblit au minimum la base métallique qui, à son tour, peut être en perlite, ferritique ou perlite-ferritique.
En raison de l'utilisation d'un traitement thermique ou d'un alliage, la base en fonte peut être aciculaire-troostite, martensitique, austénitique.
Les qualités de fonte ductile varient, maisEn général, sa désignation est la suivante: HF 40-5. Il est facile de deviner que VCh est une fonte à haute résistance, le nombre 40 est un indicateur de résistance à la traction (kgf / mm2), numéro 5 - allongement relatif, exprimé en pourcentage.
Fonte malléable
La structure de la fonte ductile est la présence dec'est du graphite sous forme floconneuse ou sphérique. Dans le même temps, le graphite floconneux peut avoir une dispersion et une compacité différentes, ce qui, à son tour, a un effet direct sur les propriétés mécaniques de la fonte.
Dans l'industrie, la fonte ductile est souvent produite avec une base ferritique, ce qui offre une plus grande ductilité.
L'apparence de la fracture de la fonte ductile ferritique a un aspect velouté noir. Plus la quantité de perlite dans la structure est élevée, plus la fracture deviendra légère.
En général, la fonte malléable est obtenue à partir de pièces moulées de fonte blanche en raison d'un mijotage prolongé dans des fours chauffés à une température de 800 à 950 degrés Celsius.
Aujourd'hui, il existe deux méthodes de fabrication de la fonte ductile: européenne et américaine.
La méthode américaine consiste à faire fondre l'alliage dans du sable à une température de 800 à 850 degrés. Dans ce processus, le graphite est situé entre les grains du fer le plus pur. En conséquence, la fonte devient visqueuse.
Dans la méthode européenne, les pièces moulées languissent dans un ferminerai. La température est d'environ 850 à 950 degrés Celsius. Le carbone est converti en minerai de fer, grâce auquel la couche superficielle des pièces moulées est décarburée et devient molle. La fonte devient malléable et le noyau reste cassant.
Marquage en fonte malléable: КЧ 40-6, où КЧ est, bien entendu, en fonte malléable; 40 - indice de résistance à la traction; 6 - allongement relatif,%.

Autres indicateurs
Quant à la division des fontes par résistance, la classification suivante s'applique ici:
- Résistance typique: σv jusqu'à 20 kg / mm2.
- Augmentation de la résistance: σw = 20 - 38 kg / mm2.
- Haute résistance: σw = 40 kg / mm2 et plus haut.
Selon leur ductilité, les fontes sont divisées en:
- Non ductile - allongement inférieur à 1%.
- Faible teneur en plastique - de 1% à 5%.
- Plastique - de 5% à 10%.
- Augmentation de la plasticité - plus de 10%.
En conclusion, je tiens également à souligner que même la forme et la nature de la coulée ont un effet assez significatif sur les propriétés de toute fonte.